For the general public, the appearance of various household appliances, car interiors, smart homes, electronic consumer goods, etc. that we commonly use is the first factor that attracts attention. The unique appearance design (high value) is more attractive to users, and at this time, our product appearance design should be more "eye-catching". In the plastic industry, smart surfaces can be used for any product surface in multiple fields such as home appliances, automobiles, medical devices, consumer electronics, OA, etc. The commonly used processes for smart surfaces include IMR, IME, IML, etc.
-In mold transfer technology (IMR)-
IMR in mold transfer technology is the process of printing decorative and functional patterns onto a foil film using a high-precision printing machine. The foil is then fed into a dedicated molding mold for precise positioning through a high-precision foil feeding device. The pattern on the foil film is then transferred to the surface of the plastic product through the injection of high temperature and high pressure from the plastic raw material.
▲ IMR process products can achieve any pattern, color, gradient, gold plating, silver plating and other effects on the surface of the product. Compared to other processes, IMR process products are more "eye-catching"
-In mold electronic technology IME-
IME is a technology that combines traditional in mold decoration (IMD) processes with electronic printing, and integrates circuit printing, mounting (electronic components), high-pressure molding, punching, and injection molding into an intelligent surface technology.
▲ Plastic products with IME technology can achieve interactive functions
IME intelligent surfaces can replace mechanical buttons to achieve a minimalist appearance or panel. Replacing static display buttons, reducing display size and cost, and implementing new touch sensitive display shapes; By sensing beneath the solid-state surface, removing bulky knobs and controllers, more complex interactions can be achieved.
-IML technology for in mold inserts-
IML technology is used to print film, which is then formed by a molding machine, cut, and placed into an injection mold for production. The prominent feature of its technology is that the surface is a hardened transparent film, the middle is a printing pattern layer, and the back is a plastic layer. Due to the ink being sandwiched in the middle, the product can prevent scratches and friction on the surface, and can maintain a bright color for a long time without fading.
Plastic products made with IML technology have high clarity in surface product patterns and colors, and are rich in three-dimensional sense;
The above are the most common surface intelligence technologies, as well as processes such as IMT and ATS. Each technology has its own unique advantages and different application ranges, but they all create excellent product appearance parts for us, bringing us a different life experience.
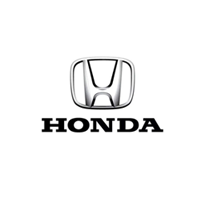
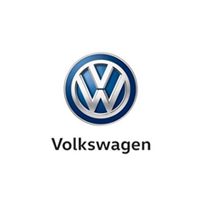
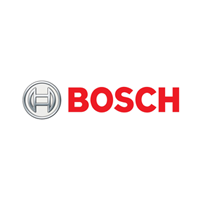

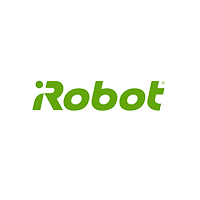
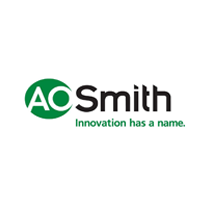

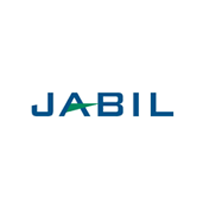
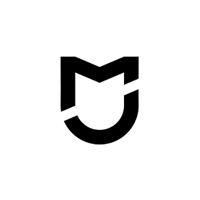
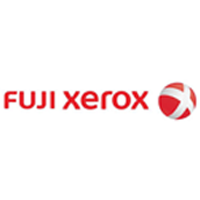
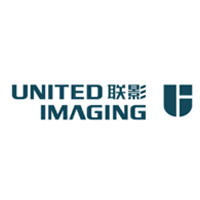
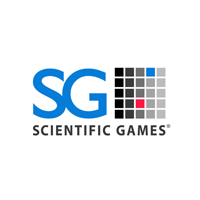
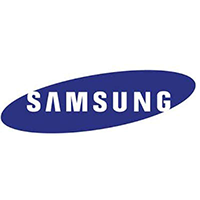
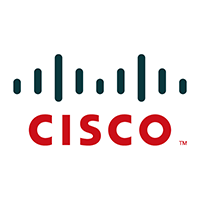
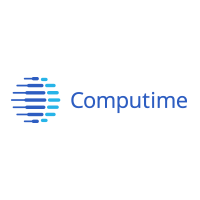
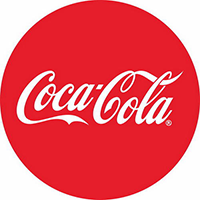
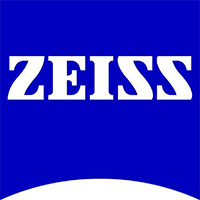

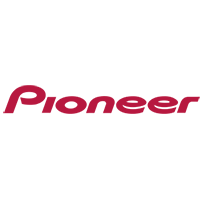






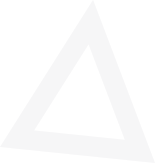
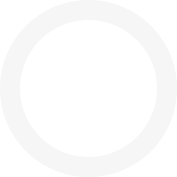
Please feel free to consult us!
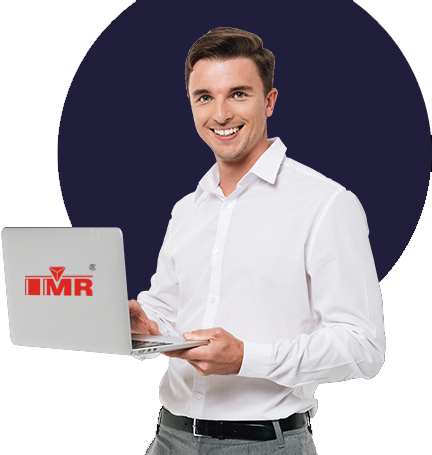