Injection molding surface decoration technology, namely IMD (In Mold Decoration), is currently a popular surface decoration technology in the world, which is mainly applied to the surface decoration and functional panels of household appliances, and is often used on the panels and signs in various fields such as mobile phone window lenses and shells, washing machine control panels, refrigerator control panels, air conditioning control panels, automobile instrument panels, and rice cooker control panels.Difference between in-mould technology IMD, IMR, IML?
IMD is also divided into IML (IMF) and IMR. The biggest difference between these two processes is whether there is a transparent protective film on the product surface.
The Chinese name of IML (IN MOLDING LABEL, no stretching, small curved surface, used for 2D products): injection molding of insert in mold. The process is characterized by that the surface is a layer of hardened transparent film, the middle is a printing pattern layer, and the back is a plastic layer. Since the ink is sandwiched in the middle, the product can prevent the surface from scratching and abrasion resistance, and can keep the color bright and not fade easily for a long time.
IMF (IN MOLDING FILM, suitable for high tensile products, 3D products) is the same as IML.
Chinese name of IMR (In-Mould Decoration by Roller): In mold transfer technology. This process is to print the pattern on the film, fit the film with the mold cavity through the film feeder for injection molding, separate the patterned ink layer from the film after injection molding, leave the ink layer on the plastic part and obtain the plastic part with decorative patterns on the surface. There is no transparent protective film on the final product surface, and the film is only a carrier in the production process. However, the advantage of IMR lies in its high degree of automation during production and low cost of mass production.
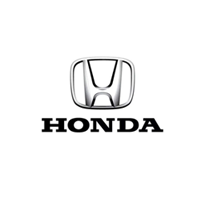
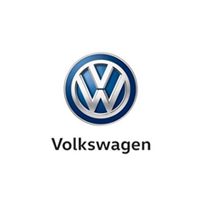
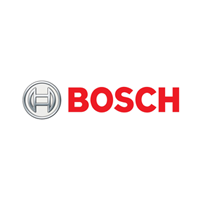

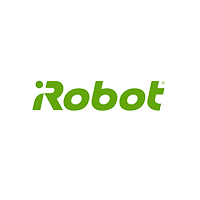
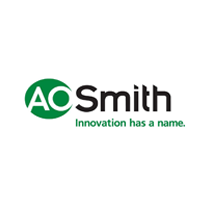

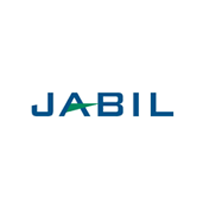
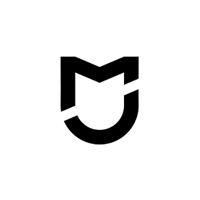
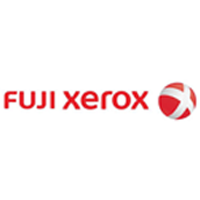
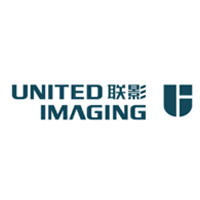
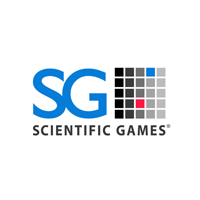
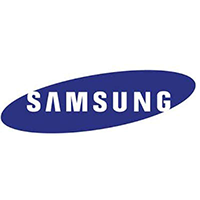
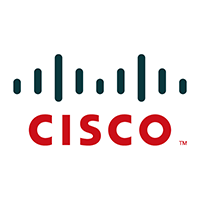
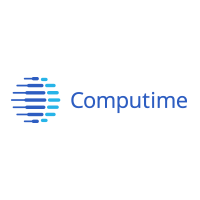
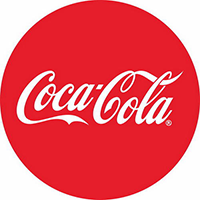
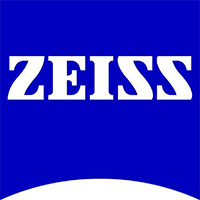

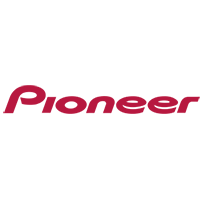






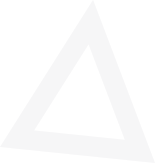
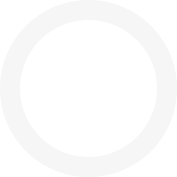
Please feel free to consult us!
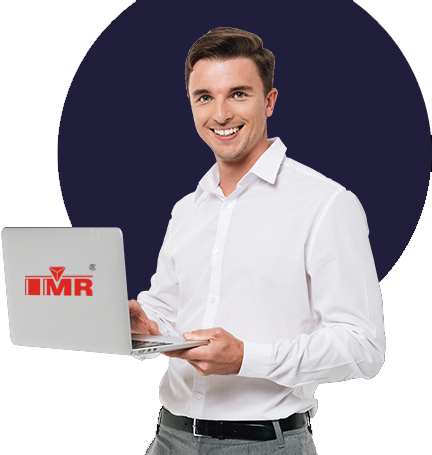