In mold injection technology IMD is a whirlwind blowing to China's plastic surface technology industry in recent years. It is a challenge to most traditional plastic surface treatment technologies such as coating and other industries. IMD industry is a high-cost and profitable industry. As a global IMD high-end brand of in mold decoration, how to succeed in this industry depends on whether you can control the cost? How to choose raw materials? How to improve skills? How to reduce the process defect rate? How to get a reasonable quotation, etc.
Imd/iml/imf defect rate is mainly controlled in the printing and shooting parts. The selection of film forming equipment also determines the stability of film forming, that is, an important factor of yield. At present, film forming equipment mainly includes hot press, air suction forming machine, and high-pressure gas forming machine, and their prices vary greatly. Generally, the price of hot press is about several thousand yuan, and the price of vacuum machine depends on its function, ranging from tens of thousands to hundreds of thousands of yuan, High pressure gas forming machine is an imd/imf/iml equipment in recent years. It first developed from the United States and Germany to Taiwan. The equipment in the United States is more than 2 million yuan, the equipment in Germany is more than 3 million yuan, and the equipment in Taiwan is about 1 million yuan. Each demand manufacturer should consider the stretching and positioning of products according to different products, different sheets used, and printed graphics and texts.
The control of IMD yield also includes the impact of the environment. We require that the whole process of IMD be carried out in a dust-free room, not to mention the printing part, and we also require it in the high-pressure forming and injection part, because the particles are easy to stick to the sheet when the sheet is heated. ".
In the injection molding of traditional products, common problems such as shrinkage, stress, flow marks and many other phenomena are inevitable in the injection molding of IMD inserts, and more new problems will appear, such as ink punching, film punching, wrinkle and so on, which are difficult to be realized only by adjusting the traditional injection parameters, because a film printed with ink is added in the mold, and its bearing temperature, pressure and time will be limited.
When ordinary PC material is used in IMD process, because of the secondary injection molding in the mold, the ink pattern on PET sheet will be dispersed. To solve this problem, the temperature of PC material cannot exceed 250 degrees. The low-temperature PC material specially developed by our company to solve the above problems can not exceed 250 degrees while increasing the miscibility of PC and pet, so as to solve the problem of ink dispersion. However, some fans said, "now ordinary PC can be used as IML, and it doesn't need low-temperature PC! We have been doing ordinary PC IML process for many years, and the injection temperature is 320! The product in the figure below is IML curler, and the high-temperature test is 100 degrees, and ordinary PC material is injected."
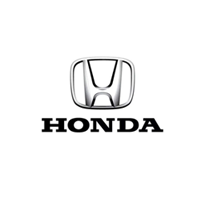
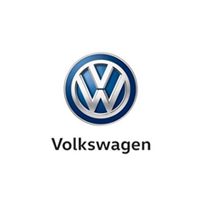
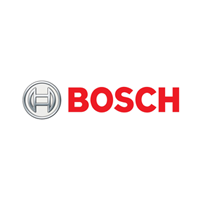

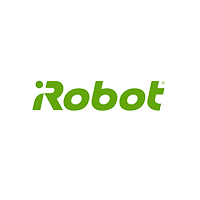
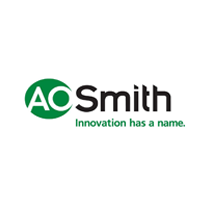

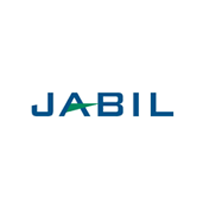
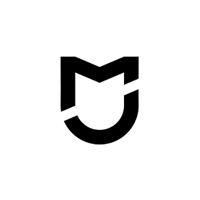
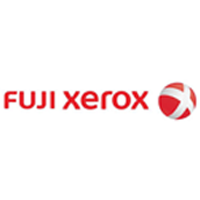
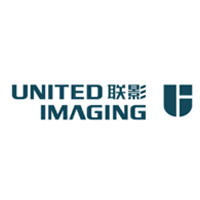
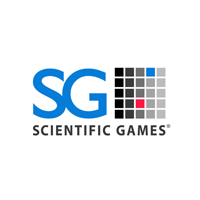
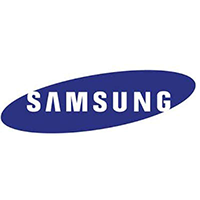
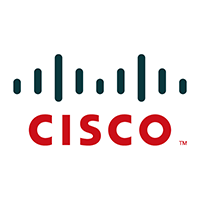
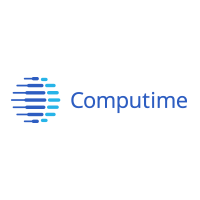
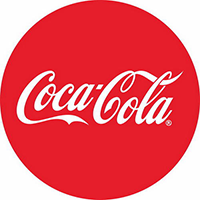
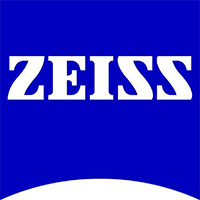

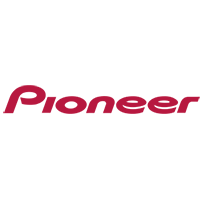






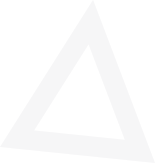
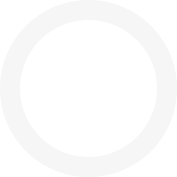
Please feel free to consult us!
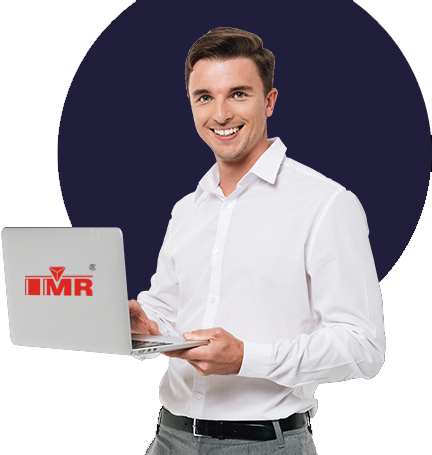