Double-sided IMR
The Double-sided IMR process involves printing decorative and functional patterns onto a foil film using a high-precision printer. Through a high-precision dual-sided foil feeding device, the foil film is accurately positioned into a specialized forming mold. Under high temperature and pressure, the patterns on the foil film are transferred onto the surface of the plastic product. The IMR foil serves as a carrier for the patterns during production, leaving no base material on the product surface.
-
The Double-sided IMR process involves printing decorative and functional patterns onto a foil film using a high-precision printer. Through a high-precision dual-sided foil feeding device, the foil film is accurately positioned into a specialized forming mold. Under high temperature and pressure, the patterns on the foil film are transferred onto the surface of the plastic product. The IMR foil serves as a carrier for the patterns during production, leaving no base material on the product surface.
In-Mold Injection Molding Diagram
Product Display
-
-
-
-
The double-sided IMR process offers diversified surface decoration.
Double-sided IMR process flow
There are two process modes for the double-sided IMR process.

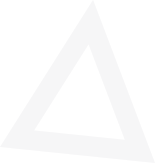
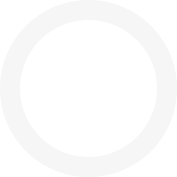
Please feel free to consult us!
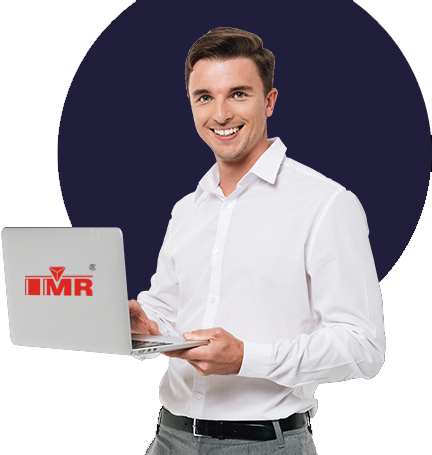